Новое решение в области производства архитектурного бетона — технология кевларобетон. Такой материал имеет глянцевую поверхность, имитирующую покрытие искусственных или природных камней либо мраморного узора. Он изготавливается методом гравитационного смешивания в специальном бетоносмесителе. Изделие имеет жесткий каркас из зерен с фракциями до 5 мм, которые обеспечивают дополнительную прочность, предотвращают растрескивание и способствуют избавлению смеси от пузырьков воздуха.
Кевларобетон называют еще ультрабетон, гранилит или окатышный бетон.
Состав стройматериала
Набор исходных компонентов и форм между тяжелым бетоном с мраморной крошкой и кевларобетоном одинаковый. Отличие состоит в подготовительном этапе перед заливкой в формы. В процессе производства получают бетонные окатыши, которые налипают на гранитный отсев. Это шарики, внутри которых плотно сцеплены крупинки песка, разные фракции отсева и портландцемента с ядром посредине. После выгрузки окатышей в формы из пластика под действием резонатора все микрочастицы стекаются в единую смесь — монолит нужного вида. А крупные частицы кевларобетона сливаются в жесткий решетчатый скелет, который влияет на свойства бетона, увеличивая показатели на излом и сжатие. Окатыш состоит из следующих элементов:
- зерно отсева с размерами до 5 мм (ядро);
- мелкие включения зерен;
- плотный конгломерат — песок, цемент, различные микрочастицы небольшого размера до 3 мм.
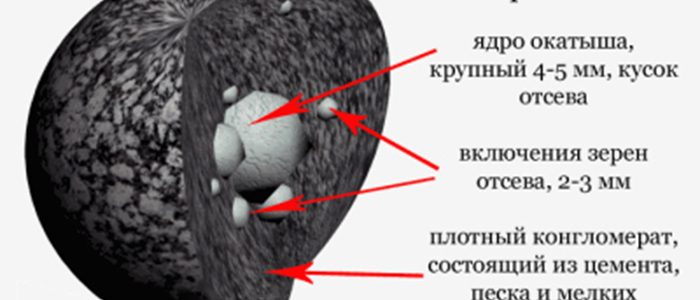
Как в любом бетонном тесте, в составе кевларобетона находится:
- минеральный крупный наполнитель с глинистыми включениями до 3%;
- гранитный отсев различной фракции, щебень или отсевы доломита, базальта;
- мелкозернистый песок;
- портландцемент марки не ниже М400 и без добавок;
- пластификатор для ускорения отвердевания окатышей (С-3 или CП-1);
- пигменты для окрашивания;
- вода затворения (массовая доля воды 17%).
Обзор характеристик и свойств кевларобетона
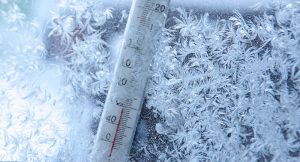
Кевлар имеет марку по прочности минимум М600 (клacc B45), это означает то, что материал способен вынести нагрузку на сжатие 600 кгс/см2. Класс морозоустойчивости кевларобетона F700, где числовое значение — это циклы попеременной заморозки и оттаивания без снижения предела его прочности больше, чем на 5%. Для сравнения большинство простых бетонов имеют морозостойкость F50-F150.
Поверхность кевлара глянцевая и гладкая на ощупь, ее секрет заключен в водоцементном соотношении материалов. Водонасыщение кевралобетона составляет 0,5% при возможно допустимом уровне 5%. При попадании воды и снега стройматериал обладает почти нулевым скольжением. Светостойкими железооксидными пигментами окрашивают изделие в любой нужный цвет и их расход как минимум в 2 раза меньше, чем при окрашивании обычных марок бетона. С помощью таких красок полностью весь раствор не закрашивается, создавая разводы с имитацией натурального камня.
В сравнении с обычными бетонными изделиями, получаемыми при помощи процесса вибролитья, изделия из окатышного бетона лучше по качеству, с высокой декоративностью и физико-химическими показателями.
Технология производства стройматериала методом гравитационного комкования
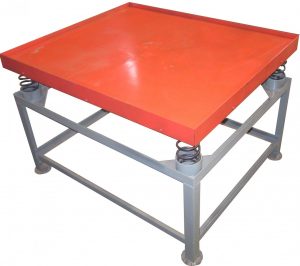
Изготовить бетон с кевларом можно своими руками, зная технологию и инструменты. Помимо изготовления бетона для своих нужд, вполне можно заняться и производством кевралобетона в качестве бизнеса. Основное оборудование — бетономешалка и вибростанок. Канализация и слив не нужны. Вложения окупятся уже за месяц производства. Для этого потребуется следующее оборудование:
- бетономешалка гравитационного типа;
- компоненты смеси;
- весы;
- совковая лопата;
- вибростол;
- пленка из полиэтилена;
- формы.
Технология производства кевларобетона выполняется по следующей схеме:
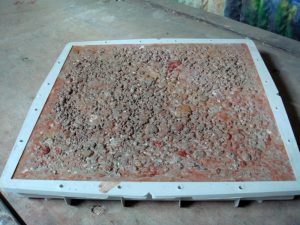
- Замес смеси. Сухие компоненты засыпают и перемешивают в бетоносмесителе не более 1 минуты.
- Добавление цемента. Добавляют портландцемент и вымешивают еще 1 минуту.
- Соблюдение пропорций, добавления пластификатора. В цементном тесте в некоторых местах движение частей замедлено, поэтому для равномерного замеса добавляют пластификатор. Его разводят в горячей воде постоянно перемешивая, чтобы он не кристаллизовался.
- Осмотр окатышей. Выборочно выбирают шарики и разбивают для оценки их внутреннего состава. Вывод о готовности смеси делают по диаметру и плотности тела окатыша.
- Ввод пигментов. После того как окончательная форма окатышей принята, добавляют краску, которую наносят только на верхний слой кевлара, уменьшая тем самым расход пигментов. Краску добавляются сухими и небольшими частями и перемешивают не более 10 секунд.
- Загрузка сырья в пластиковые формы. При заполнении формочек до 80% включают вибростолы, после чего досыпают до полного заполнения формы и накрывают плотной полиэтиленовой пленкой. Сушка происходит в течение 24 часов. После распалубки изделия должны вылежаться 5 суток.
Область использования кевларобетона с гладкой поверхностью
Основное применение — облицовка и отделка. Окатышный бетон используется для изготовления таких элементов, предметов и конструкций:
- плитка для укладки тротуара;
- заборы и элементы изгородей;
- бордюры при дорожках;
- камины;
- клумбы;
- фасадный камень;
- элементы садово-парковой архитектуры;
- ступеньки.
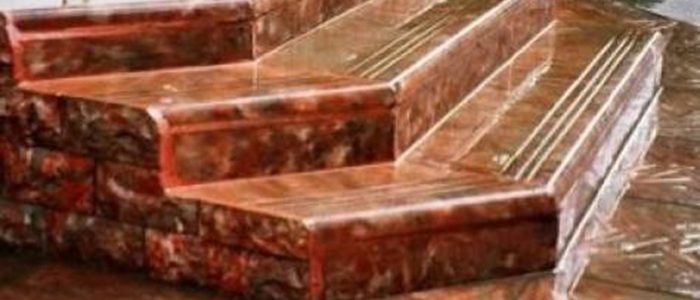
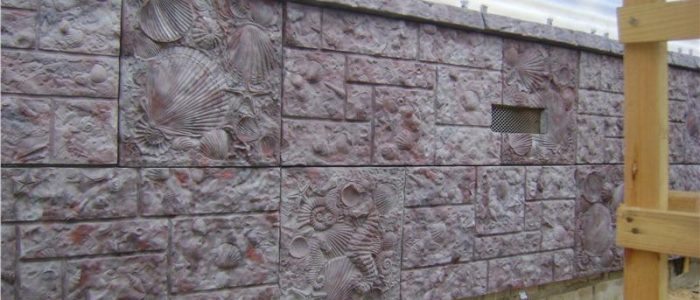
Характеристики кевларобетона по морозостойкости, истираемости и влагонепроницаемости, сопротивляемости проникновению хлоридов и газонепроницаемости делают его востребованным и популярным при оформлении фасадов, площадок для детей, архитектурных и декоративных элементов зданий и сооружений. Самое главное достоинство этой технологии — это применение обычных недорогих компонентов.